What is a shift
A shift is a core part of the last-mile scheduling process. At a minimum, it defines the earliest time deliveries can start and the latest time they can finish during the day. It is also a way to manage the number of trips a depot can run at any given time. Having shifts properly set up is essential for scheduling to work.
The core parameters of a shift include:
Each shift is transformed into a trip within the schedule. If there are 10 active shifts for a given day, there will 10 trips assigned in the Schedules screen for the corresponding day. Changing shifts impacts the draft schedules (specifically the trips) for the current and future dates.
A shift, and therefore a trip, can last up to a day. The delivery solution does not support multi-day trip planning.
Shifts are managed at a depot level.
By default, a shift will start and end in a depot unless custom start or end locations are explicitly defined. Turning on the reload configuration at a depot level enables a vehicle to be routed for a reload at a depot during shift configuration.
To set up a shift, certain information is required as a minimum. This includes: start and end times, offset and a vehicle assignment with start and end dates. The loading capacity for each individual trip is defined by the assigned vehicle’s constraints.
The same vehicle can be assigned to multiple shifts, as long as the shift hours during a specific day don’t overlap.
Shift times are the maximum possible start and end time of a trip. The actual trip may start later or finish earlier based on the volume of orders to be scheduled and the duration of travel. The optimisation engine schedules all orders and complies with the requisite shift start and end times.
There are extra and optional parameters to set too, including requirements for driver breaks, loading duration, different start and finish locations, and flags.
Flags is a helpful feature that enables you to map specific orders to specific trips. For example, very large items require 7.5t trucks to transport them. Or you may need to constrain one vehicle, or multiple vehicles, to go to one neighbourhood within a catchment area. To make this possible, flags are required for both trips and orders. Flags for trips are managed at a shift level, whilst order flags are defined during order creation (done via API or through Control Room).
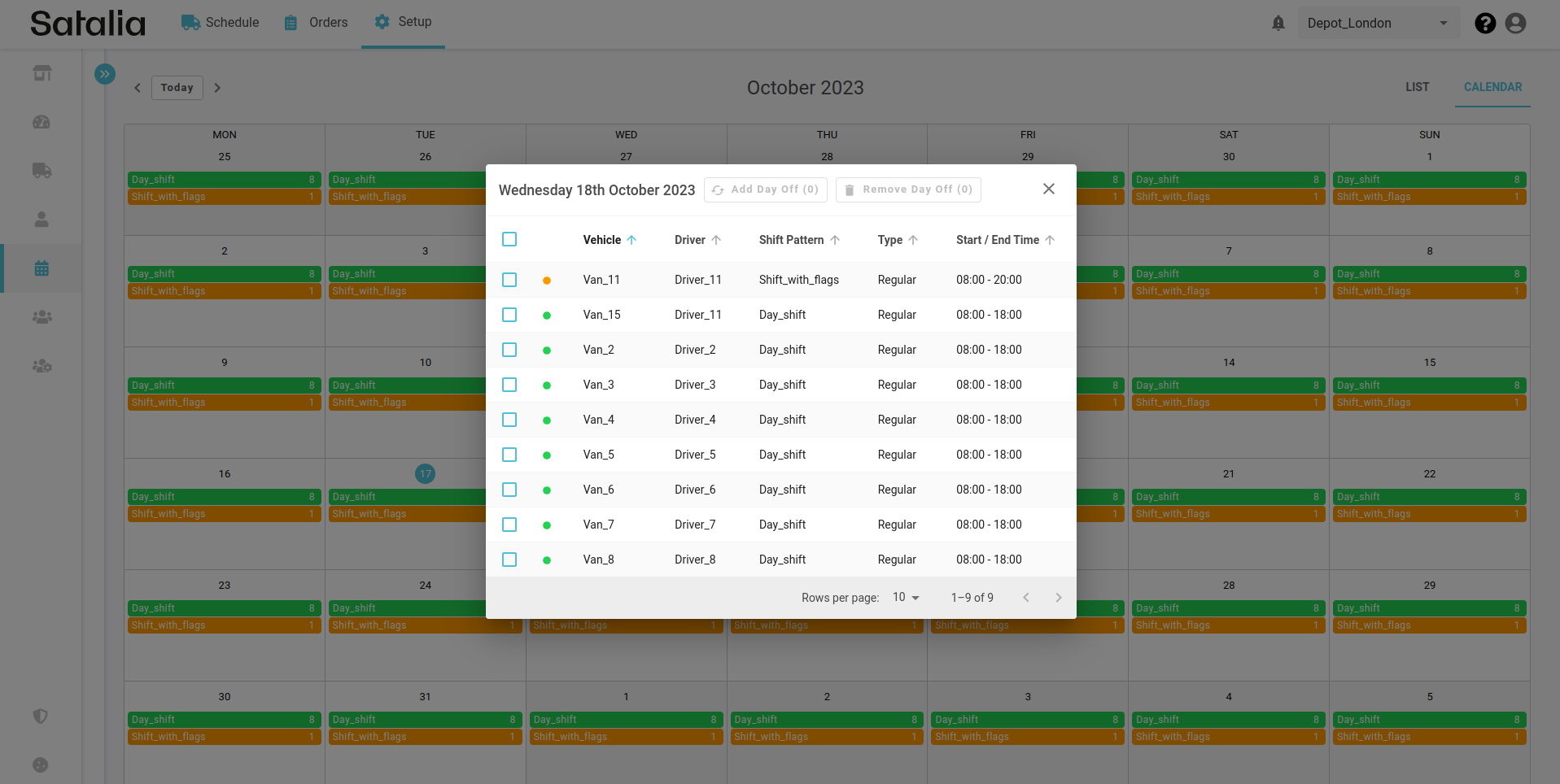
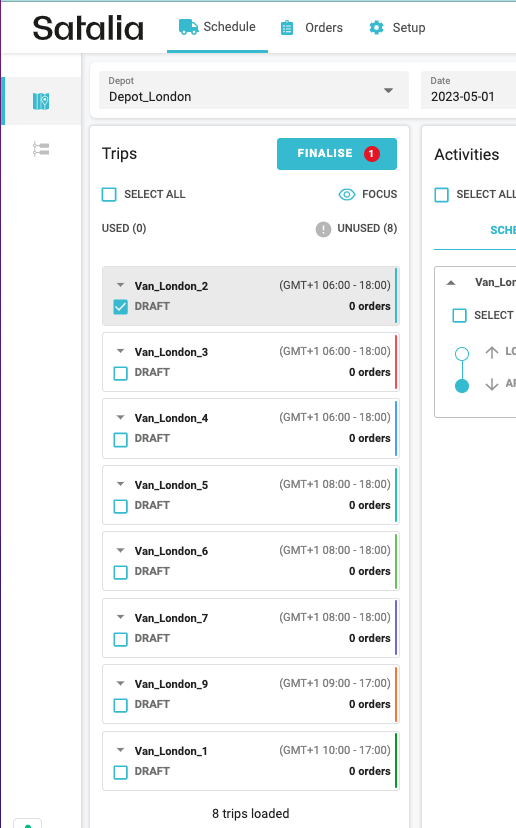
Shift creation and management is an essential process to get right, so we ensure there are multiple features within the Control Room to enhance efficiencies, including shift patterns, regular, temporary shifts and days off, calendar view, filters, and more. Discover more about them in the following articles: Introducing shift patterns, Create regular shift , Create temporary shift, Create day off.